When he makes a mistake, he realizes it.
Having realized it, he admits it.
Having admitted it, he corrects it.
He considers those who point out his faults
as his most benevolent teachers.
He thinks of his enemy
as the shadow that he himself casts.
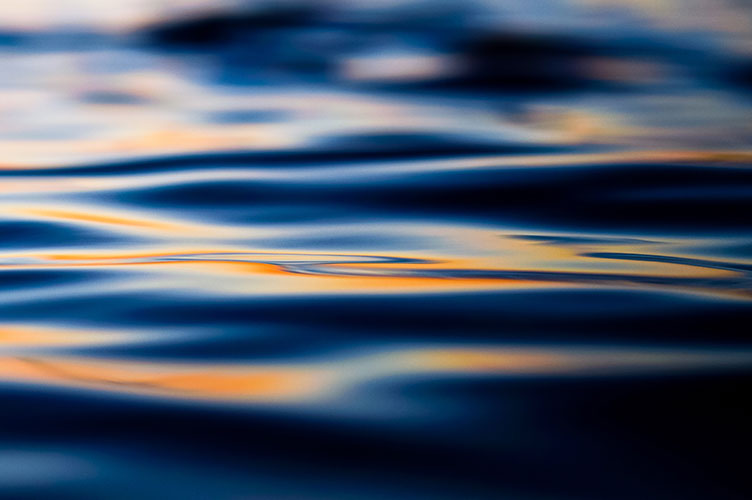
We all have them. We love to find them in others. They are often considered bad but as the Tao Te Ching points out, faults present an opportunity to learn and improve. Those that point them out and report them to us should be celebrated.
Finding faults in processes, equipment, and facilities is to be celebrated as well. Indeed, fault reporting is a core maintenance concept used to increase operational availability and reduce operating costs. Finding and resolving faults proactively provide opportunities to avoid unplanned maintenance, minimize downtime, and make preventative improvements.
Manifest has long been used by maintenance technicians and mechanics at organizations such as Jabil, the United States Army, and the New Zealand Defense Force, as another way to manage preventative maintenance. It helps make maintenance, repair, and overhaul (MRO) and inspection procedures more efficient and accurate to keep equipment operating properly and to make facilities safer and more compliant. With the latest release of Manifest, we have added new fault reporting capabilities to further improve these procedures.
Manifest’s new fault system enables workers to flag faults while performing maintenance procedures and inspections and then review and resolve these faults. Fault data becomes part of the job history so data on which faults occurred, where they occurred, when they occurred, and who resolved them are archived in the system. There is more.
- Compliance or quality checklists can be created with specific, spatially placed, instructions that can be left for follow-up and resolution of faults
- Faults can be flagged in every step of a maintenance or inspection procedure
- Custom dropdown lists of fault types or status can be configured for each piece of equipment so that faults are reported in a standard way that is consistent with reporting already used in the enterprise.
- Evidence, such as a photo, video, note, or meter reading, can be required to provide additional context about the specific fault
- All users with appropriate permissions can easily identify where issues were reported and review the faults along with any operator notes by stepping through the work instructions augmented over the location or equipment
Early customers using this new capability have reported improvements in modernizing maintenance procedures, digitizing the process of reporting and verifying faults in a compliant way, and the ability for less experienced workers to more accurately complete maintenance tasks. Additionally, customers using the fault system expect to improve their fault reporting in a few significant ways:
- Decrease delays in fault verification and repairs
- Decrease human errors when giving instructions or transferring data
- Eliminate tedious fault validation procedures
- Consolidate databases with fault and repair parts information
- Replace physical manuals
- Enable remote fault verification and support
This latest release of Manifest will make everyone an expert at fault reporting. So, the next time you encounter a fault, don’t be bashful about celebrating it. Stand up and shout “It’s all my fault”!
We are excited about this release and early customer feedback, if you would like to learn more or see a demo, reach out to us here.