Augmented reality helps scale the expertise held by an older employee or the maker of the machine by turning that expertise into software and sharing it, via heads-up displays, to any new worker.
Stacy on IoT – The “help wanted” signs scattered throughout restaurants, stores, and medical offices are becoming all too familiar these days. While economists can debate if that’s because pay is too low or pandemic benefits are too high, the end result is the same: It’s hard to find people to fill jobs.
The employee shortage issue is especially acute in manufacturing, where an aging workforce is rapidly retiring and new entrants are sparse. This lack of qualified personnel is actually a big reason factories are embracing IoT. Before COVID struck, the idea was to both attract younger workers with new technology and to reduce the number of people needed to staff factories. Today, digitization is also reducing the risk of hiring new employees while helping them quickly get up to speed on their new responsibilities. And one of the best tools for this is augmented reality (AR).
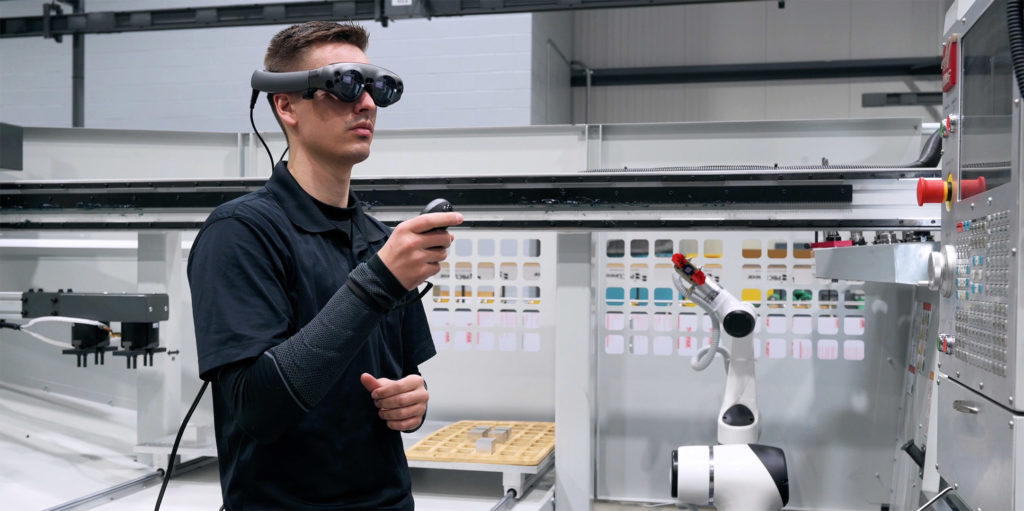
PBC Linear, a manufacturer in Roscoe, Ill., has learned how helpful AR can be after it implemented AR software and a mix of Microsoft Hololens and Magic Leap AR headsets to train new employees at the beginning of the pandemic. In March 2020, the company elected to buy software from Taqtile, a Seattle-based company, to build out the software that would run on those headsets.
Taqtile’s software helps non-experts code processes into Augmented Reality simulations. It’s like what Microsoft FrontPage did for HTML and building websites, except it’s for programming tasks and processes into code used by AR glasses. I had been really focused on AR as a way for factory workers to process a lot of information coming from digitized equipment, but was concerned that actually building the software to train employees would take way more work than it was worth, especially for highly specialized machining tasks.
One of the challenges associated with AR has been in trying to turn a complex physical process, such as wiring a component or working a machine, into code that could run on a headset. Taqtile CEO Dirck Schou said the company’s software makes programming for AR glasses simple, and based on my conversation with Tim Lecrone and Beau Wileman of PBC, the software Taqtile developed is easy to use. Once PBC has created a module for training it pays for itself after 1.44 employees train with it according to Wileman.
At PBC Linear, there used to be an employee available to train a new worker on equipment and processes over a period of four to six weeks. But as the company’s staff began to retire and COVID affected its workforce, PBC needed more new employees than it had senior staff to train them. And the numbers were only going to get worse. So Lecrone and Wileman decided to invest in digitizing their operations.Â
Their digitization plan involved placing sensors on the equipment, adopting cobots to handle certain processes, purchasing both AR gear and the Manifest software from Taqtile, and hiring college-aged interns interested in machining.Â
The first set of interns was able to build out AR flows that showed how to operate each machine as well as workflows to program the cobots that would also operate machines alongside people. The interns also needed to build AR flows for the people who would need to work alongside the cobots. In August of this year, after implementing the AR and cobots, PBC also purchased sensors from a company called Reply to track when their machines were on or off.
Wileman said the sensors are fairly simple and they were easy to deploy. He assigned a new crop of interns to place them on machines in the factory so PBC could track when machines went offline. Because many parts of the company’s manufacturing process require the product to move from one machine to another, having the ability to track when the process stopped or slowed is valuable.Â
The cobots help handle processes that are repetitive and free up people to take on different tasks. Given how tough it is to hire people to work in the factory, using them helps reduce the overall staffing load. But the biggest gains so far have been in training and getting employees quickly up to speed. Now PBC can hire a person and get them working on a machine in a few days as opposed to that taking up to six weeks. It also helps reduce the cost of training a cobot and staff. Wileman told me that an intern, which costs $17 an hour, can train a cobot or map out a process in less than four hours, while it might cost around $30,000 for an outside expert to manually train a cobot.Â
Plus, when building out the models or training, the new employees enjoy using headsets, said Wileman. It’s not just the younger employees that use them; older employees like them as well. He said that many of the staff are gamers, so they are familiar with the tech and enjoy it. The ability to speed up training is only one benefit. It also makes it less painful when a newly trained employee decides to leave.
Lecrone told me that the PBC factory is on a stretch of road where several other manufacturers have their operations, and it’s pretty common to hire and train someone only to see that person leave for a job up the road for higher pay or a larger signing bonus. But while that stings, a newly trained employee leaving no longer represents as much of a drain on an existing PBC employee’s time or the company’s resources.
Wileman said that the company hires some 50 new people a year and saves about $1,200 per employee in training costs. So while PBC still has a hiring challenge, it is able to use IoT, robotics, and AR to get new staff trained more quickly and at a lower cost, which makes it less painful when those staff members eventually leave.Â